If you are working with a pharmaceutical or semiconductor manufacturing cleanroom, you most likely have seen ultrapure water in action. This water is used for water for injectables (WFI) in pharmaceuticals and as a chisel for semiconductors. While it has many other purposes, these are the primary two.
And those two industries use a lot of ultrapure water!
For example, processing a single wafer uses over 1,000 gallons of ultrapure water. For many cleanrooms, that means going through hundreds of thousands of gallons of water every year. Thus, having a system that creates the water for you is paramount for many organizations. But what is the process of making and storing ultrapure water? Let’s talk about it.
How To Make Ultrapure Water
The production of ultrapure water is broken into three phrases: pretreatment, primary, and polishing.
The first consideration is the feed water. Per the United States Pharmacopeia guidelines, you should start with easier basic purified water or drinking water. You should always consider where the water comes from and the changes it might experience through the seasons.
The first step of the pretreatment phase is to put the water through a basic filter to remove any large debris. While these debris might be nearly microscopic, in the cleanroom world, they are considered relatively large.
Once the water has been filtered, it is time for either two pass Reverse Osmosis, Demineralization and Reverse Osmosis, or High Efficiency Reverse Osmosis (HERO). You might also incorporate Activated Carbon or sodium bisulfite to dechlorinate the water. This is a mixture of physical and chemical processes to eliminate contamination from the water.
Osmosis is when water is forced through a semipermeable membrane to remove contaminants. Reverse osmosis occurs when the water is forced in the opposite direction of natural osmosis. Activated carbon works through absorption of particles. Sodium bisulfate is used to control pH levels.
The next phase is the primary treatment phase. This phase uses ultraviolet light and electrodeionization or a mixed bed ion for maximum demineralization. You might also use dissolved oxygen removal through a membrane or vacuum degasification.
Ultraviolet light essentially kills contamination. The energy from the light enters the particle and damages the microorganisms internal structures. Mixed bed ion uses chemicals to pull ionized particles from the feedwater, but electrodeionization is a chemical-free and continuous process that serves as an alternative to accomplish the same task. It is typically used in combination with reverse osmosis.
The last stage of creating ultrapure water is the polishing stage. This is the most important but often most expensive step in the process. This step once again uses ultraviolet light along with heat exchange to control the temperature in the ultrapure water supply. Because ultrapure water is typically made in very large quantities, changing the temperature of this amount of water can be taxing.
Lastly, non-regenerable ion exchange with membrane degasification and ultrafiltration finalize the water filtration to reach the required particle level.
And, with that, the ultrapure water is ready to be put to work in your cleanroom!
How To Store Ultrapure Water
As ultrapure water is created in a very specific way, there are also very specific ways to store the water. Here are a few to keep in mind:
- Your entire system – including your storage – needs to be completely sealed from potential contamination.
- If the water stays still for too long, it will stagnate which can produce contamination in the word. Thus, it is important to constantly maintain water flow.
- To reduce microbial growth, the temperature should be controlled constantly through heat exchangers or a plant room for cooling. The guidance value for this is < 25.328 °C.
- At strategic storage locations, there should be ultraviolet disinfection.
- The components should also be thermally or chemically sanitized regularly.
At the end of the day, the most important thing is protecting the water from microbial contamination or recontamination. This can be prevented through proper storage and monitoring.

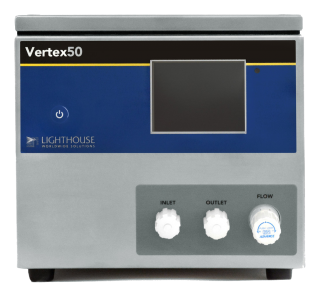
How To Monitor Ultrapure Water For Contamination
Certain ambient-temperature systems, like reverse osmosis, ion exchange, and ultra filtration, are susceptible to contamination. This is especially true when the systems are less utilized, such as when the demand for water is down.
During this whole process, the water should be routinely checked for contaminants, but especially at the end. Very simply put: you cannot use the water nor will you know that you have achieved the necessary levels of cleanliness without checking your water with a liquid particle counter.
A liquid particle counter forces a sample of water through either a laser or general light source, depending on the technology used and size of particles allowed. The light displacement tells the particle counter the size and number of particles present in the sample, which allows you to know your contamination level.
When using a liquid particle counter, you will need to first determine the level of cleanliness your water needs to achieve. If you need to monitor your water down to the nanometer particle, you will need a light scattering liquid particle counter with a partial stream laser. If you are doing water in large bulk and the smaller particles are permitted, then a light blocking particle counter will be sufficient.
At the end of the day, you don’t have to look far for the liquid particle counter that leads the industry in zero count levels, size, and reliability. Based on state-of-the-art technology, the Vertex 50 by Lighthouse Worldwide Solutions is backed by a two-year warranty and international support.
If you want to schedule your hassle- and obligation-free consultation, contact us today.