Gas Sampling in Cleanrooms
In cleanrooms, especially those classified ISO 5 or cleaner, maintaining contamination control is paramount. One significant potential source of contamination is compressed gas. Proper gas sampling is crucial in these environments to ensure that the compressed gases used do not introduce particles that could compromise the cleanroom’s integrity. The international standard ISO 8573 provides comprehensive guidelines for gas sampling in cleanrooms, ensuring compliance and optimal performance.
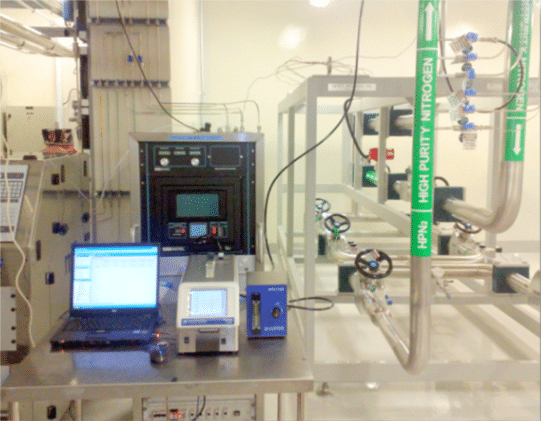
The Role of Compressed Gases in Contamination Control
Compressed gases can introduce a variety of contaminants into a cleanroom, including particulate matter, moisture, and oil. To mitigate these risks, it is essential to continuously monitor and sample these gases, as part of the overall contamination control plan. The 2022 update to the GMP Annex 1 emphasizes the need for a risk-based approach to contamination control, requiring higher testing standards and stringent monitoring practices.
ISO 8573: The Standard for Gas Sampling
ISO 8573 is the international standard for testing compressed gas, oil, and water in cleanroom applications. It comprises nine parts, with the most recent update in 2010, and outlines acceptable testing methods and limits. ISO 8573-1:2010 is particularly important as it specifies contamination limits for particles, water, and oil in compressed gases.
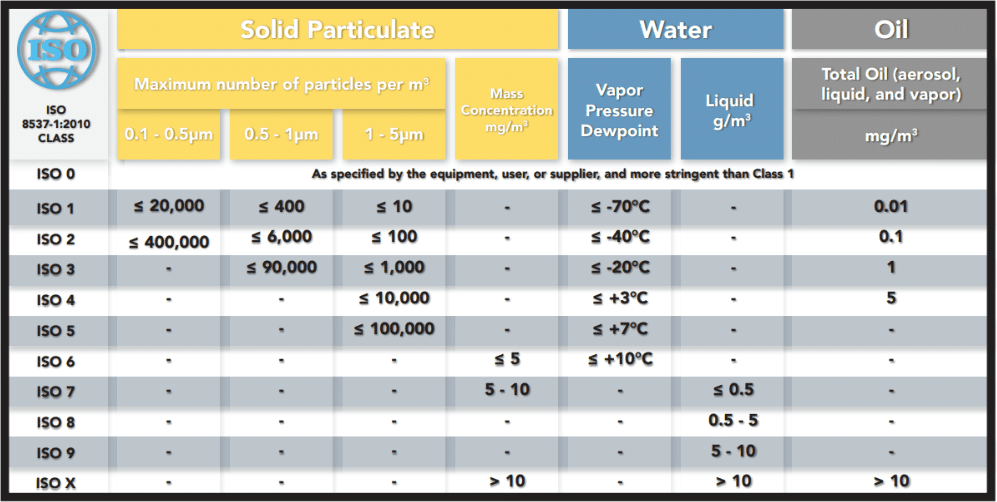
Tools for Gas Sampling
According to ISO 8573, two primary tools are used for gas sampling: particle counters and active air samplers.
Particle Counters
Particle counters are essential for measuring particle concentrations in compressed gases. These devices must maintain isokinetic sampling to ensure accurate measurements. Isokinetic sampling prevents skewed particle concentrations by maintaining consistent gas velocity throughout the sampling process which is at the same flow rate as the particle counter which keeps the sampling accurate. High-pressure diffusers (HPDs) are used to achieve this consistency, with vented return and ported exhaust options available depending on the type of gas.
Active Air Samplers
Active air samplers, such as the Lighthouse ActiveCount100H, offer a versatile and effective method for gas sampling.
Industry Applications
Various industries, including pharmaceuticals, food and beverage, and electronics, must comply with ISO 8573 standards for gas particle concentration monitoring. In the technology sector, where smaller particle sizes (down to 0.1 µm) are critical, advanced setups like the High-Pressure Controller combined with the SOLAIR 1100 LD particle counter are used. This setup allows for precise sampling in high-purity environments, ensuring compliance with ISO 8573 Class 0 standards.
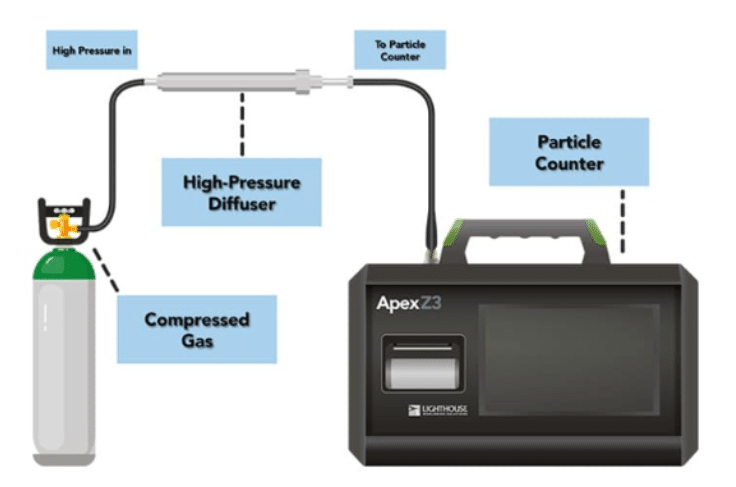
Conclusion
ISO 8573 provides essential guidelines for testing compressed gases in cleanrooms, addressing both viable and non-viable particle contamination. Implementing these standards is crucial for maintaining cleanroom integrity and ensuring compliance with evolving regulations. Whether using particle counters or active air samplers, it is vital to choose the right tools for your specific needs.
Lighthouse Worldwide Solutions offers industry-leading options for gas sampling, designed to meet regulatory requirements and keep your cleanroom environment pristine. For more information on cleanroom technology and its applications, visit our Knowledge Center.
By incorporating comprehensive gas sampling into your contamination control plan, you can safeguard the integrity of your cleanroom and ensure the highest standards of cleanliness and compliance.