GAMP5 refers to the fifth publication of Good Automated Manufacturing Practices published by the International Society for Pharmaceutical Engineering (ISPE). GAMP5 is not a set of regulations, but instead a collection of guidelines developed through evidence-based decision making that reinforces the standards set by many regulations, including Annex 11 and 21CFR11. These guidelines outline a risk-based approach to determining quality throughout the entire production process.
This is a part of GAMP5’s unique and holistic approach: quality control and validation should be included in every step of the production process. This comprehensive approach is beneficial far beyond the pharmaceutical industry. Thus, GAMP5 is technically made for pharmaceutical manufacturers but we see it referenced in a wide range of industries.
A Brief History Of GAMP5
The original set of GAMP guidelines was published in 1991. Since then, it has undergone 5 revisions with the most recent revision being published in 2008. The last revision made major changes to include collaborations with regulatory agencies, such as the United States Food and Drug Administration (FDA). This was done in an effort to create guidelines that reflected major regulatory changes throughout the world.
Implementing A GAMP5 RTMS
To sum GAMP5 up: it is essentially a risk-based, holistic approach to implementing a Real Time Monitoring System (RTMS) throughout the entire production that creates a traceable, automated, and repeatable process. It is the core of computerized system validation.
To demonstrate the implementation of GAMP5, we will use the GAMP V model, as shown in Figure 1.1. This model flows from the top left to the top right with corresponding verification across the V. Implementing a GAMP5 RTMS is broken down into 4 phases.
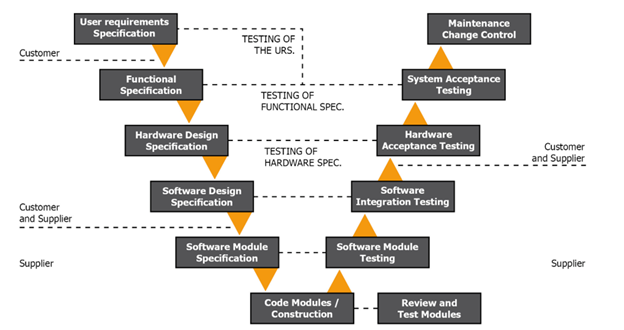
GAMP Phase 1
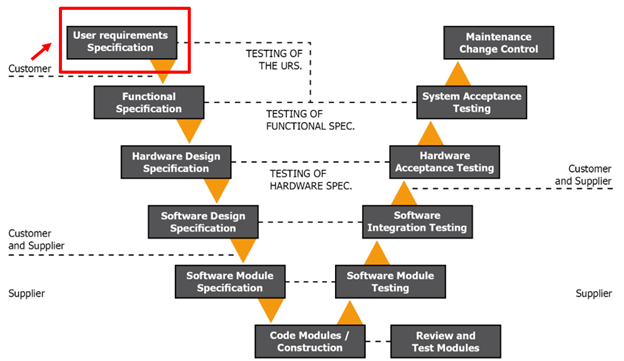
The first portion of the V model covers the groundwork needed to implement a RTMS, which is perhaps the most important step. GAMP5 covers the science-based Quality Risk Management (QRM) analysis that should be done during this process. You should bring together a team of experts who understand your process and RTMS to help with this. This allows you to develop proper User Requirement Specification (URS) based on science and your quality risk management.
A strong URS is the starting point and ending point of a RTMS and any other computerized system you add. Here at Lighthouse, we have basic URS templates we offer customers so they can have a well-rounded starting point. It is fundamental to this process, as you will notice throughout the V model.
Once you develop your URS and supply it to your vendor, they will determine if the requirements are sufficient. It is important you consider the URS traceability matrix.
GAMP Phase 2
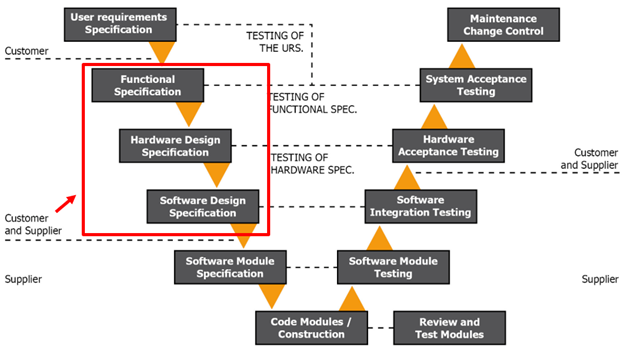
At this point, you should have chosen a vendor and have an approved URS. During Phase 2, you will develop the Functional Specification (FS) using the HW and SW specifications and the URS. You will use the FS to illustrate how the RTMS will operate and be designed and configured. It will also show which HW and SW will be used. You must identify all components of the RTMS, including the integration modes and communication (i.e. sensor accuracy, traceability, and adherence to cleanroom and calibration standards).
GAMP Phase 3
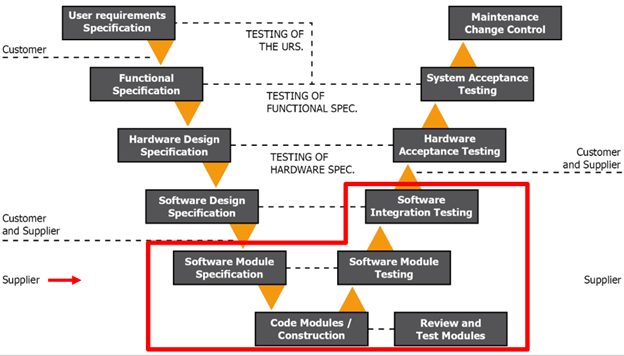
Phase 3 demonstrates how to assemble your system based on your URS and FS. You will put together your sensors, system modules, digital output devices, serial to internet converters, software, database configurations, and any other configurations. This phase is primarily your vendors’ responsibility with some input from you. Occasionally, you may change your mind during this process or decide to add more functionality, so we encourage you to regularly meet with your vendor for design reviews before the system is completely developed. This eliminates surprises.
We also recommend having all stakeholders and end-users involved. This is a large investment that is not taken lightly or done regularly, but many people are impacted. For instance, IT departments are heavily impacted but often not included in the process. They should be engaged from the start.
GAMP Phase 4
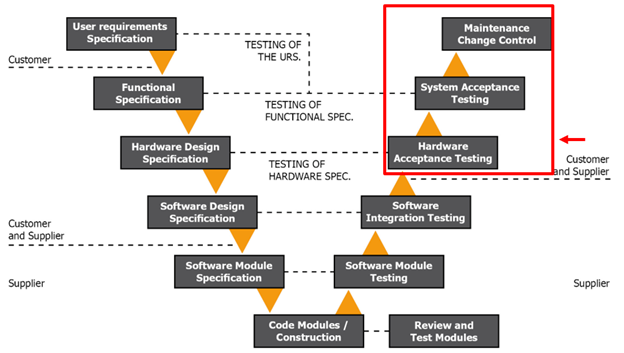
At this point, your system has been developed and internally tested. Now, during phase 4 of the V model, we are back at your site where the system is installed and commissioned.
During this phase, you will run acceptance testing of the system. These tests include SAT, IQ, and OQ testing. These validate your system as fit for use. All testing should be traceable back to the URS.
Once the testing is complete, you are ready to take ownership of the system and test it in your business environment. This is a real manufacturing, production environment. You can run simulations and the Performance Qualification (PQ).
While not listed in the V model, you should conduct a PQ once the vendor hands over the system. It would fit under the System Acceptance testing. To conduct a PQ, you run the system to failure and develop Standards Of Operation (SOPs) to respond to the failures. Your PQ is your opportunity to test the system during real life scenarios. You will answer questions such as:
- How does management respond?
- How do technicians respond?
- How does the vendor handle software failure?
- How is data integrity maintained?
Your PQ should not be a simple re-run of the vendor’s OQ. The PQ is your last chance to truly adjust and change the system and develop very comprehensive SOPS before you go live.
Once the PQ is complete, it is time to train the operators and system owners. Humans make or break a RTMS, so their training is vital. GAMP guidelines, as well as other best practices and certifications, require regular personnel training. We encourage different levels of training, as well, depending on the individual’s role in the cleanroom environment.
Finding the Right Vendor
As you can see, following GAMP5 when it comes to implementing a RTMS does not fall solely to you. Thus, you should work with a vendor who also follows GAMP5 practices. If you want to know how our team implements GAMP5 into our practices, feel free to contact us.