In 2017, GMP released a draft update to Annex 1, which received a lot of feedback. Now, GMP has released a finalized version of the updated Annex 1, which addresses many of the concerns and questions raised about the draft version.
The largest changes and shifts in this document are found in the increased focus on Quality Risk Management (QRM) through a comprehensive Contamination Control Strategy (CCS). As always, GMP’s goals are to provide safe products and keep people healthy. Technological advances have decreased the need for manual interventions and humans on the manufacturing or filling line. The minimization or elimination of personnel can drastically reduce the risk of contamination, but does require changes to SOPs and documentation. With more technology, how you maintain audit trails must be adjusted to ensure all the information and data integrity remains.
GMP Annex 1 is comprised of 10 parts that address aseptic processes for pharmaceutical products, although many portions of this document serve as excellent guidelines for other industries. This blog post is the second part of our series breaking down the basics of each of the 10 parts and highlighting some notable changes to theory and practice. Part 1 covers the first 5 parts and this blog post will cover the last half: parts 6 through 10.
GMP Annex 1 Part 6
Part 6 of GMP Annex 1 discusses utilities in cleanrooms, specifically those that come into contact with the final product and pose a risk of contamination. For example, water and steam. It also lists the utilities you should keep records of through the lifecycle of the room.
This portion of the document specifically addresses 4 utilities: water systems, steam used for sterilization, gasses and vacuum systems, and heating, cooling, and hydraulic systems.
Water is perhaps the most intensive utility, as water for injectables (WFI) is subject to strict standards. This does discuss the production and storage of WFI, as well as the importance and design of water treatment plants.
Steam should come from a source with water held to the same standards as WFI. It should not contain additives that could cause harm to the product.
Gasses that come into contact with the product should be filtered and monitored appropriately. All relevant parameters, such as oil contact, should be recorded and taken into account.
Lastly, heating, cooling, and hydraulic systems should, whenever possible, be located outside the cleanroom.
GMP Annex 1 Part 7
Part 7 outlines the regulations surrounding personnel in cleanrooms, including training on gowning and conduct in cleanrooms. While Annex does not define a time between training periods, it does dictate training should be conducted “regularly” and stresses the importance of understanding.
This section goes on to outline gowning best practices and the general expectations from humans, including communication if their health changes, good hygiene, and the types of clothes to be worn (or not worn) under sterile gowns depending on the level of cleanroom they are working in.
In keeping with the theme of decreasing reliance on humans in a cleanroom, we are also instructed the lowest number of humans possible should be present in any given clean zone. Additionally, the maximum number allowed should be recorded during the design of the cleanroom.
This portion of Annex 1 shows additional changes from previous versions. There is a heightened focus on personnel knowledge in cleanrooms, which is also reflected in part 3.
GMP Annex 1 Part 8
Section 8 is the most comprehensive portion of Annex 1, as it actually outlines the production of sterile products and the associated technologies. This portion specifically addresses:
- Terminally sterilized products
- Aseptic preparation and processing
- Finishing of sterile products
- Sterilization
- Sterilization by heat
- Moist heat sterilization
- Dry heat sterilization
- Sterilization by radiation
- Sterilization with ethylene oxide
- Filter sterilization of products which cannot be sterilized in their final container
- Form-Fill-Seal (FFS)
- Blow-Fill-Seal
- Lyophilization
- Closed systems
- Single use systems (SUS)
For each of these facets, we see a heightened emphasis on incorporating the CCS throughout. Depending on your process and technology used, we’re seeing changes in requirements for pre-use post sterilization integrity tests (PUPSITs), specific processing holding times, visual inspections, reinforced sterility test sampling after critical interventions, and container closure integrity.
GMP Annex 1 Part 9
Section 9 is perhaps one of our favorite sections here at Lighthouse Worldwide Solutions: environmental and processing monitoring. From the start, we see a much larger focus on the inclusion of the CCS in your environmental monitoring, which typically includes total particle monitoring; viable particle monitoring; temperature, humidity, and other specific characteristic monitoring; and Aseptic Process Simulation (APS) monitoring.
This part of Annex 1 outlines exactly how you should be monitoring your cleanroom – and documenting it for all of the listed factors. For different grades of cleanrooms (Grades A, B, C, and D, with A being the cleanest), different monitoring protocols should be in place. For example, it is required Grade A clean zones be monitored continuously for total particles.
We also get a detailed list of items to be considered in the design of your APS. While the APS alone should not verify the cleanroom, it is a critical check done regularly and should be treated as such.
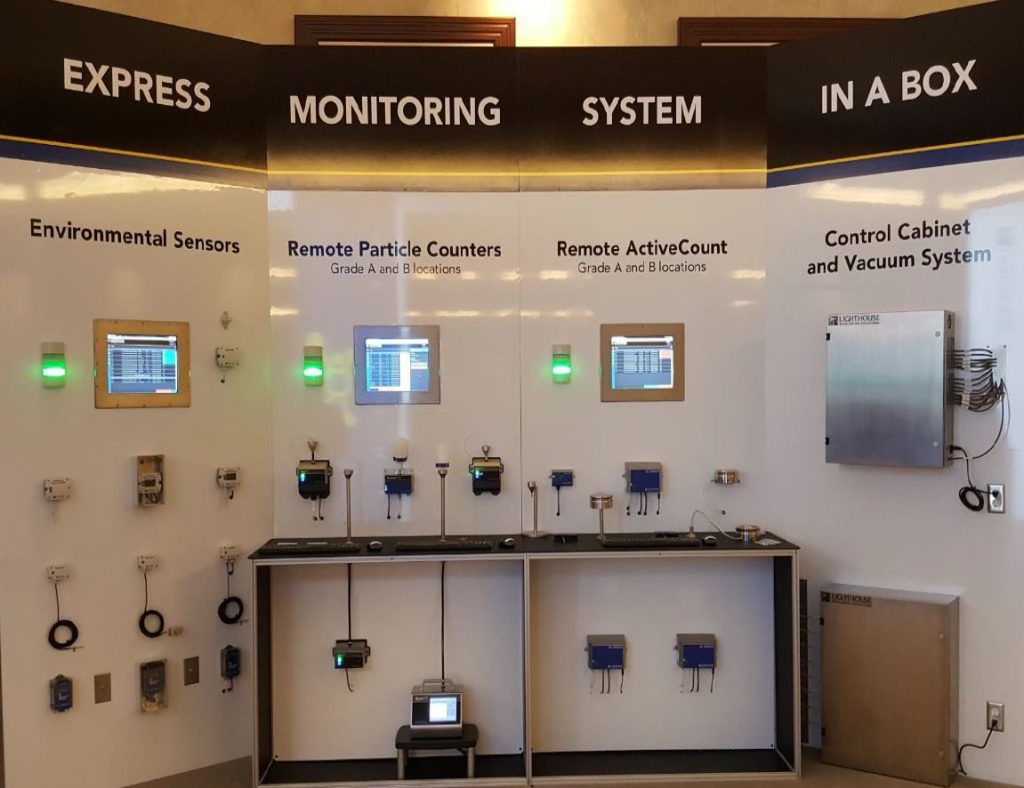
GMP Annex 1 Part 10
Lastly, Annex 1 covers Quality Control (QC), where we see the shifts this document has taken. This includes the focus on comprehensive personnel knowledge and development around the CCS. Overall, the new draft of Annex 1 increases the testing burden and decreases the number of personnel who should be physically involved in sterile processes.
Are You In Compliance?
With these changes to GMP Annex 1, many organizations will face an institutional and infrastructural adjustment to comply with heightened regulations surrounding your Contamination Control Strategy. The good news is that we are the world’s experts on clean air and building a comprehensive CCS.
If you have any questions about this new version of GMP Annex 1 and how it will impact you, talk to our team of specialists today.