The article is mainly focused on the impact, causes and reduction of particle generation during the manufacturing of Li-ion cells. Therefore, it is sub-divided into three sections as each aspect is equally important to study the topic in detail. Sections are listed below.
1. Effect on the cell
2. Sources of generation
3. Mitigation techniques
We are going to start with the first section i.e.; effects of particle generation on cell, in order to understand the need to study this topic. This section will establish the strong WHY to delve well into the topic.
Effect on the cell
Let us consider the typical 21700 Li-ion cell with NMC as a cathode material and graphite as an anode material with Aluminum and Copper as a current collector respectively. Any impurities (foreign particles) present inside the cell affects the cell capacity and performance drastically. To understand the concept well let’s see what causes cells to fail to meet their functional requirement.
- Internal Short circuit (ISC)
We know that the cell is layered structure of active material with some binders, conductive agents coated over a current collector. Both the electrodes are separated by the separator made up of non-conducting material in order to avoid the direct contacts. Direct contact between the electrode results in the internal short circuit (ISC) of the cell.
If we consider the structure of lithium ion cells, there are four different mode of contact responsible for ISC. They are mentioned below.
a. Cathode – Anode
b. Cathode – Copper foil
c. Anode – Aluminum foil
d. Copper foil – Aluminum foil
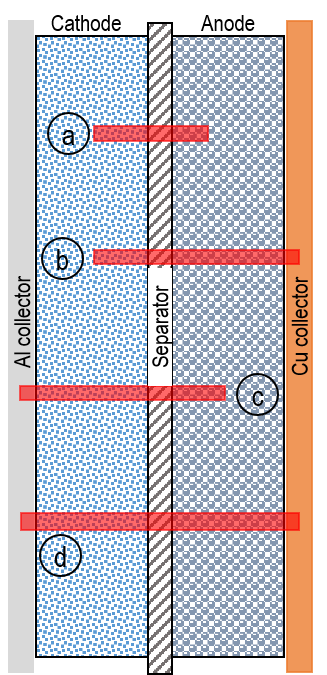
In a good quality cell, all the surfaces are properly separated and positioned so that the probability of ISC is almost negligible. But when the impurities are present on the cell layers, it acts as medium that causes the short circuit in the cell.
This raises a question: How can a particle cause the surfaces to come in direct contact? When the particles are trapped inside the cell during the manufacturing phase, it can cause damage to the separator by penetrating into it and making a path for the electrodes and current collector to come in contact with each other. This defect will be reflected during the inline short circuit test of the cell.
During charging, high current flows through the cell and causes a sudden short circuit inside the cell resulting in a heat generation which can lead to a fire and explosion in the charging chamber.
- Voltage drop
In another way, these particles are also responsible for voltage drop during discharge of cells by causing an increase in the internal resistance of the cell. Internal resistance is the resistance that the cell offers to flow of current. This resistance is very small, but when there are particles present on the layer of electrodes they create a microstructure that can increase the resistance – leading to a voltage drop of the cell.
Both of the phenomenon explained above result in “not good” (NG) cells during the production. This directly impacts the overall yield of the factory.
- Dendrite Formation
If the size of these particles is very small, they are often undetected during all the inline inspections and cells are considered good cells and are used in the completed battery pack. Then with use, one more phenomenon takes place called a lithium dendrite formation. It takes place as a result of the difference in rate of transfer of lithium ion from cathode to anode, and the diffusion rate of lithium ion towards the center of anode particles. So, metallic lithium is formed and grows as the time passes.
By offering a physical base for dendrite growth, these particles give dendrites the nucleation site they need to develop on once they start to form. It speeds up dendritic development and causes an early loss of battery capacity.
Source of particle generation
When it comes to generation of particles in a manufacturing plant, there are many potential sources causing it. Even particles of a few micron in size can cause deteriorating effect on the cell.
The major factors that are responsible for the generation of particles includes personnel, process equipment, leakage in the dry room and malfunctioning of AHUs.
Personnel: Personnel presence inside the dry room is considered the main reason for generation of particles. The human body generates millions of dead skin cells every day which can contribute to the particle intrusion. During breathing, particles get airborne due to exhalation. Hair dandruff can also be the reason for the generation of particles. While performing routine tasks inside the dry room particles become airborne due to body movements of the operators.
Process Equipment: During production, the cell is processed through various steps such as electrode preparation which comprises of mixing electrode powder, coating and calendaring, slitting and drying. Second step is the winding and assembly of the cell. The last step is cell finishing. All the equipment for this process has one or other moving parts that can be responsible for generating particles due to abrasion and wearing of moving parts. Other operations like the cutting processes, and welding processes can also contribute to particle generation.
Leakage in the dry room: Leakages can be another factor contributing to particle generation. During the construction of the dry room, as a result of negligence or improper commissioning there can be some leakages present in the walls, through which particles can sneak in and contaminate the environment. Over a period of time the degradation of wall material can also lead to formation of leakages.
Malfunctioning of AHUs: All dry rooms are required to be maintained at specific environmental conditions. Incoming air needs to pass through series of devices such as dehumidifier, cooling coils, dampers and air filters. Damage to any of these components results in a variation of air quality and unwanted particles which can enter the dry room causing contamination in the environment.
So far we have gone through effects and sources of particle generation and understood how important it is to keep track of them. In order to do that, let’s discuss methods to mitigate the cause of particle generation.
Mitigation techniques
In this section, we will go through standard protocols followed for particle monitoring in manufacturing factories. ISO 14644 is the international standard specifically made for dry rooms.
In order to have the least probability for generation of particles inside dry rooms, strict protocols must be followed by all the operators working in the equipment. We will cover one by one various methods implemented throughout the industry for tracking and managing the generation of particles.
Personal protective equipment (PPE): All the operators working inside the dry room must wear the proper PPE kit as defined in their protocols before entering the room. Everyone must pass through the air showers installed near the entrance of room. Operators must make sure that all the body parts are covered except nose. While working inside the dry room, operator should not move rapidly as this causes particles to become airborne. Operators should be properly trained for working inside the dry room so that they follow strict discipline during the work.
Particle count monitoring: According to ISO 14644, cleanrooms are defined on the basis of ISO classes ranging from 1-9. ISO class 1 is the most stringent class whereas class 9 is the least stringent. These classes have a predefined limit for the number of particles of particular size to be allowed inside the room.
The room is divided into number of zones where the particles are counted with the help of an optical particle counter and reported. In this way, any malfunction happening inside the room is reflected into the report, and necessary actions can be taken to address the issue. Particles can be monitored in real time as well as periodically depending upon the company.
Dust collectors: Processes such as cutting, slitting and welding generate particles and these are detrimental to the product. So, a dust collector creates a vacuum suction and sucks in the particles keeping the product safe.
Cleaning and mopping: Products such as mops and wipes should be cleanroom compatible and properly sterilized before use. Personnel responsible for the cleaning must be trained with the correct protocols and should adhere to them every time the cleanroom is cleaned. Floors are mopped with a cleanroom specific detergent and HEPA filter vacuum. Walls are wiped with a damp sponge and then vacuum dried. The frequency of cleaning depends on the ISO class maintained inside the room and protocols defined by the company.
Monitoring of AHU system: Regular checks must be conducted for testing the functionality of AHU as it directly supplies the air to the cleanroom as per the ISO specification. When there is increase in the particle generation, periodic air flushing must be performed in order to supply the fresh air and take out the contaminated air.
Apart from above techniques, a dedicated team should be assigned to conduct the testing of samples and report the cause of the particle generation. This way the exact issue can be focused and addressed.
Author: Ankit Fule