Ensuring Cleanliness and Product Quality
Keeping precision parts free from contamination is crucial in industries like aerospace, automotive, semiconductors, and medical devices. Even the smallest particles can impact performance, reduce product lifespan, or, in the case of medical implants, pose serious health risks.
To maintain high cleanliness standards, manufacturers use strict cleaning processes, often shifting to water-based solutions due to environmental regulations. But even with the best methods, how can they be sure parts are truly clean? That’s where Liquid Particle Counters (LPCs) come in.
Why Liquid Particle Counters Matter
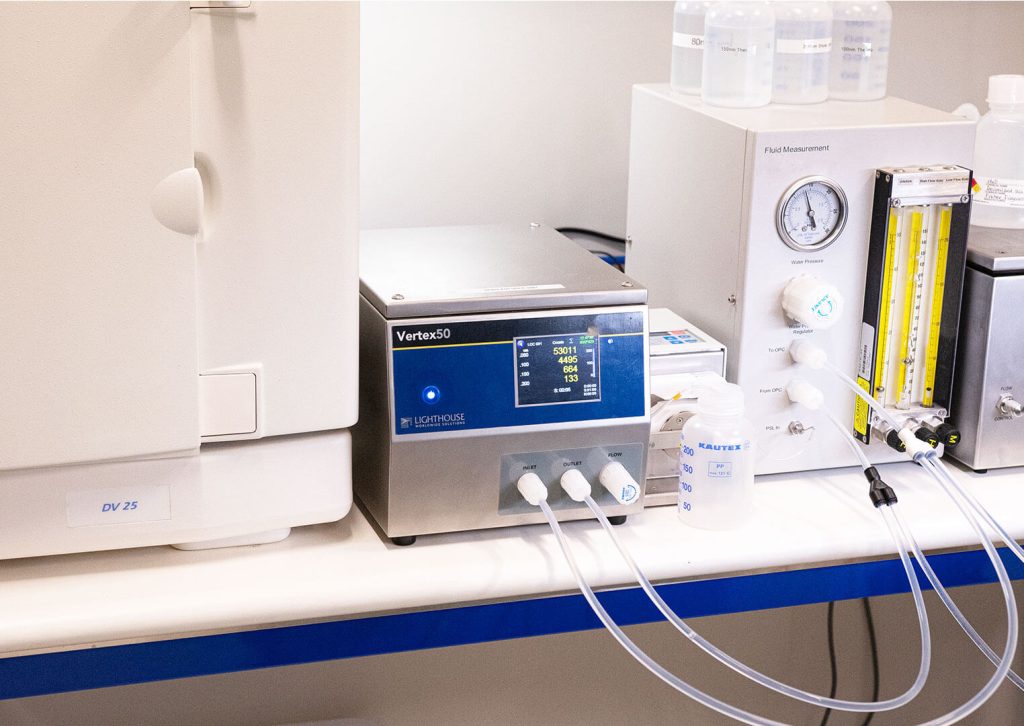
LPCs are essential tools for real-time contamination monitoring in cleaning solutions. These devices provide immediate feedback, helping manufacturers verify cleaning effectiveness. Advanced models like the Lighthouse Vertex50 offer 50nm sensitivity, allowing continuous inline monitoring for improved contamination control.
How Industries Clean Precision Parts
Different industries use specialized cleaning methods to remove contaminants, and LPCs validate each process to ensure parts meet strict cleanliness standards:
Ultrasonic Cleaning
Uses high-frequency sound waves to create tiny bubbles that dislodge contaminants from complex surfaces.
- Industries: Semiconductors, Aerospace, Medical Devices, Automotive, Data Storage
- LPC Validation: Measures particle levels in the cleaning solution to confirm thorough cleaning.
Immersion Cleaning
Submerges parts in a solvent or water-based solution to dissolve contaminants, often paired with ultrasonic cleaning.
- Industries: Semiconductors, Aerospace, Medical Devices, Automotive
- LPC Validation: Measures particle levels before and after cleaning to ensure effectiveness.
CO₂ Cleaning
Uses dry ice or liquid CO₂ to remove contaminants without leaving residues.
- Industries: Semiconductors, Medical Devices, Aerospace, Data Storage
- LPC Validation: Confirms no residual particles remain.
Passivation
Removes ferrous particles from stainless steel to improve corrosion resistance, following standards like ASTM A380 and A967.
- Industries: Aerospace, Medical Devices
- LPC Validation: Verifies complete particle removal.
Where LPCs Make a Difference
LPCs are used in a wide range of industries to verify cleanliness and improve quality control:
- Aerospace: Optical sensors, turbine blades, fuel system components
- Automotive: Fuel injectors, brake components, transmission parts
- Medical Devices: Heart valves, catheters, surgical implants
- Semiconductors: Silicon wafers, photomasks, chip packaging
- Data Storage: Hard disk drives, magnetic heads
The Bigger Picture:
Why LPCs Are Essential
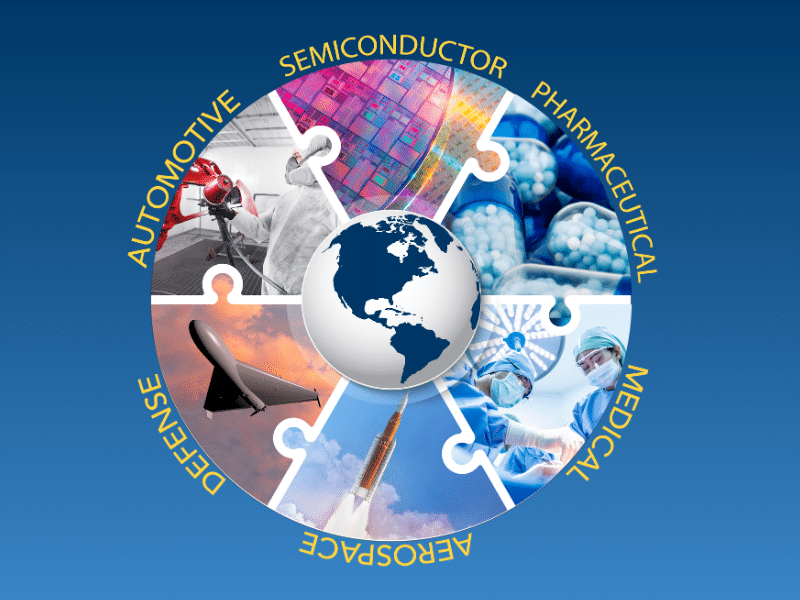
LPCs do more than just monitor cleanliness—they help manufacturers:
- Meet regulatory standards by ensuring compliance with industry cleanliness requirements
- Improve quality assurance by reducing contamination risks
- Optimize processes with real-time monitoring and data-driven improvements
- Protect cleanroom environments by preventing cross-contamination
- Strengthen customer confidence with superior cleanliness standards
Conclusion
From ensuring medical implants are safe to protecting semiconductor performance, Liquid Particle Counters are a must-have for precision parts cleaning. By adopting LPC technology, manufacturers can guarantee product reliability, regulatory compliance, and top-tier quality.
Want to improve your contamination control? Fill out the form below and we’ll have someone from our team contact you!