Introduction
In the high-stakes realm of Pharmaceutical manufacturing, precision and adherence to stringent cleanliness standards are non-negotiable. Compressed gases are a staple in cleanroom environments, but they also present a potential risk of contamination. This article delves into the pivotal role of compressed gas sampling in pharma cleanrooms, emphasizing the unique challenges and regulatory considerations faced by this industry. We’ll explore ISO 8573, the international standard for gas sampling, and specialized tools and techniques tailored to Pharma’s specific needs.
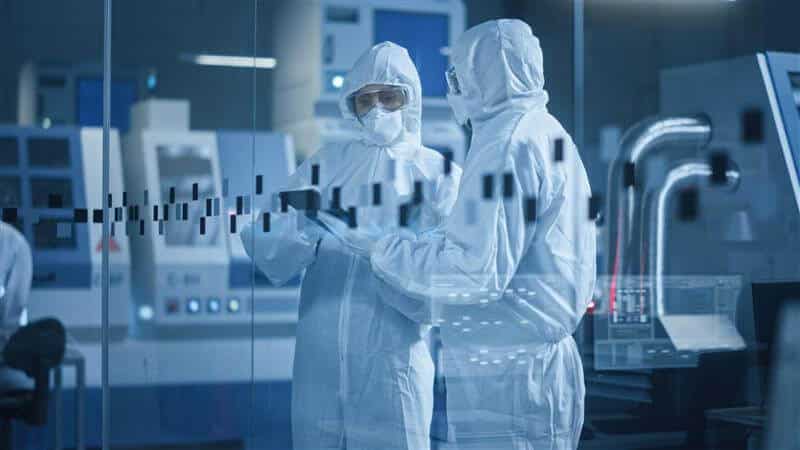
The Pharma Imperative for Gas Sampling
In Pharma cleanrooms classified ISO 5 or cleaner, even the tiniest particles can spell disaster for product quality and patient safety. Compressed gases, including oxygen, hydrogen, methane, and nitrous oxide, are potential carriers of contamination. Therefore, meticulous monitoring of these gases is an indispensable aspect of any contamination control plan within the biopharmaceutical sector.
Recent years have witnessed the emergence of more comprehensive contamination control plans, driven by increasingly stringent regulations. For instance, the 2022 update of GMP Annex 1 underscores the importance of constructing cleanrooms based on risk-based contamination control plans. These plans necessitate a holistic approach, including the vigilant monitoring of compressed gases—an area meticulously regulated by ISO 8573.
Deciphering ISO 8573
ISO 8573 stands tall as the international standard for testing compressed gases, oils, and water in cleanroom applications. Comprising nine parts, with the most recent update in 2019, this document serves as a beacon for maintaining contaminant-free cleanrooms. Related blog: Basics Of ISO 8573.
The linchpin of ISO 8573 is often ISO 8573:1-2010, a section that outlines how to represent contamination in terms of ISO cleanroom classifications. These classifications are denoted by three numbers, each signifying particle, water, and oil measurements.
For instance, consider ISO 8573-1:2010 Class 1.2.1 cleanroom. It adheres to class 1 particulate measurements, class 2 water measurements, and class 1 oil measurements. Particle measurements reflect the quantity of particles present in one cubic meter of compressed air or gas. Water measurements pertain to pressure dewpoint, while oil measurements denote permissible oil content in each cubic meter of air.
Specialized Tools for Gas Sampling
In the context of ISO 8573 guidelines tailored to pharma, two primary tools are indispensable for measuring contamination in compressed gases: particle counters and active air samplers. Let’s explore these tools and their applicability in pharma cleanrooms.
Particle Counters: ISO 8573 recognizes particle counters as a valid method for testing compressed gases, but with specific requirements. Crucially, particle counters must maintain isokinetic sampling, a technique that prevents skewed particle concentration measurements due to inertia. Achieving isokinetic sampling entails the use of a high-pressure diffuser (HPD).
High-Pressure Diffuser (HPD): ISO 8573 mandates the use of high-pressure diffusers (HPDs) to ensure isokinetic sampling. There are two primary types of HPDs: Vented Return HPDs and Ported Exhaust HPDs. The choice depends on the type of compressed gas in use. Vented Return HPDs release gas back into the environment, while Ported Exhaust HPDs expel air outside the cleanroom—an essential safety measure when dealing with potentially hazardous gases in the presence of open flames.
Active Air Sampler: Active air samplers present an alternative solution for gas sampling that can obviate the need for additional attachments like an HPD. Notably, the Lighthouse ActiveCount100H simplifies gas sampling. This user-friendly device facilitates gas sampling by utilizing a fresh Petri dish without agar, snugly attaching the gas sampler to the sampling head, and optimizing the flow rate for gas sampling. Related video: https://youtu.be/VoPX6XURgw0?t=3
Active air samplers also play a pivotal role in situations where viable contamination is a concern. While particle counters provide data on particle quantity and size, active air samplers can discern particle types, including viable particles capable of growth and replication—an essential consideration in pharma applications.
Applications in Pharmaceutical Cleanrooms
The need for compliance with ISO 8573 standards for gas particle concentration monitoring extends to various industries, with biopharmaceuticals leading the charge in precision and contamination control. Here are some tailored applications within the biopharma sector:
Pharmaceutical Technology: In the technology-oriented biopharmaceutical sector, the emphasis is on sampling smaller particle sizes, down to 0.1 µm, in compressed gases. The most advanced setup involves a High-Pressure Controller in conjunction with a Solair 1100 LD (0.1 – 5.0 µm) particle counter. This setup, designed for gas lines with pressures between 2-10 bar, enables the sampling of 0.1 µm particles at ISO-1 (8573-1) levels—an indispensable requirement for maintaining product quality.
Viable Contamination Control: Pharma cleanrooms must be vigilant against microbiological contamination in compressed gases. By utilizing Lighthouse’s ActiveCount100 in tandem with a gas sampler adapter, biopharma professionals can connect the device to gas lines with pressures ranging from 2-10 bar. This setup streamlines the process and ensures effective viable contamination monitoring.
In Conclusion
Gas sampling in pharma cleanrooms is not merely a compliance requirement—it’s a vital element of contamination control that safeguards product quality and patient safety. ISO 8573 provides indispensable guidelines and regulations for this crucial task, ensuring alignment with industry standards and regulatory expectations.
Whether through particle counters or active air samplers, the choice of tools and techniques must align with specific biopharma needs. Lighthouse Worldwide Solutions offers comprehensive solutions designed to meet regulatory standards and uphold the sanctity of pharma cleanroom environments. By adhering to ISO 8573 and leveraging specialized tools, biopharmaceutical manufacturers can fortify their commitment to product integrity and a controlled production process.