What happens if an injectable is contaminated? Infections, complications, vein irritation, local tissue infarction, anaphylactic shock, other health risks, and potentially death… The end-user is put in jeopardy. That is why it is vital we prevent contamination at the source: in the cleanroom during the manufacturing of the pharmaceuticals. This involves utilizing a liquid particle counter to check the liquid for contamination.
The Food and Drug Administration (FDA) is the responsible authority for monitoring the cleanliness of injectables. They define the standards and good manufacturing practices (GMPs). They also have developed the United States Pharmacopoeia, which is a guide defining the production of pharmaceuticals to prevent contamination.
We define particles in injections as extraneous, mobile, undissolved particles that are unintentionally present in the end product. They can come from a myriad of sources, including packaging materials, cleanroom personnel, and different ingredients. But no matter where it comes from, the presence of particles is hazardous to the end-user.
In the manufacturing of these medicines and devices, it is critical we adhere to these guidelines to prevent yield loss, fines, costly process redesigns, and, most importantly, health complications.
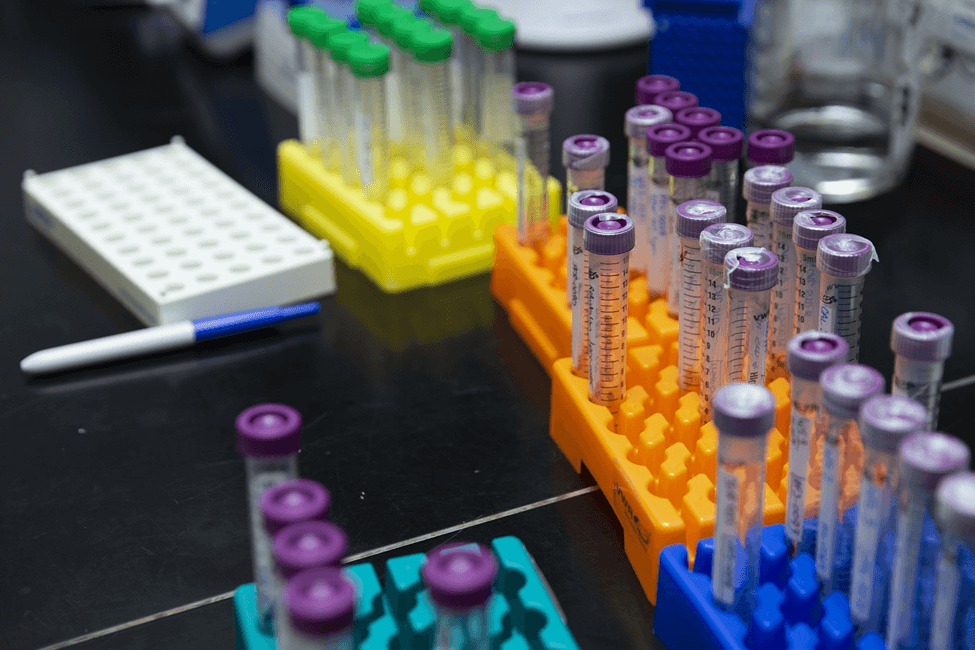
What Is USP <788>?
The United States Pharmacopoeia 788 (USP <788>) defines the standards for testing water for injectables (WFI) developed in cleanrooms. This standard defines two ways to test for particles: light obscuration and microscopic assay. Typically, water is first tested using light obscuration. If the liquid fails the parameters using light obscuration, a microscopic assay is used as a secondary testing measure.
There are two ways to package this WFI: large volume parenteral (LVP) and small-volume parenteral (SVP). LVP means that the injectable is packaged in a single-dose vial containing 100ml or more of the solution, whereas SVP contains less than 100ml. Both light obscuration and microscopic assay are accepted testing methods for determining if there are sub-visible particles present.
USP <788> Validation Requirements
USP <788> requires validation of your liquid particle counter every six months. The liquid particle counter is what is used to conduct the particle checks, although we’ll talk more on exactly how that works in just a moment.
To validate liquid particle counters, we commonly use Count-Cal particles manufactured by Thermo Scientific. They are designed to fit into the National Institute of Standards and Technology’s (NIST) traceable diameters. Their accuracy is 3000/ml ±10%. This allows you to calibrate your equipment within USP <788> standards. Because the validation testing requires several tests, you are able to document that your liquid particle counter is able to replicate the correct readings. This is an important part of documenting your traceable GMPs.
Your liquid particle counter must be calibrated at your location – and then not move from that spot – according to USP <788>. The basic requirements for validation include:
- Sample volume verification
- Volume accuracy test
- Sample flow rate verification
- Sensor calibration
- Sensor resolution test (10µm test particles)
- Count ratio test: blank test using clean, particle-free water
- Count ratio test: 15µm Count-Cal reference particles (3000/ml ±10%)
The validation is complete when the liquid particle counter is able to pass the count ratio test using 15µm particles. From there, the corresponding counts need to fall in between 2,700 and 3,300 particles. There is an allowance for a ±10% tolerance at 3,000 per milliliter. This is both a simple and effective validation of the liquid particle counter sensor’s accuracy!
How Liquid Particle Counting Works
Light obscuration is the primary method for testing for the presence and size of particles. This is similar to light scattering that is used in airborne particle counting.
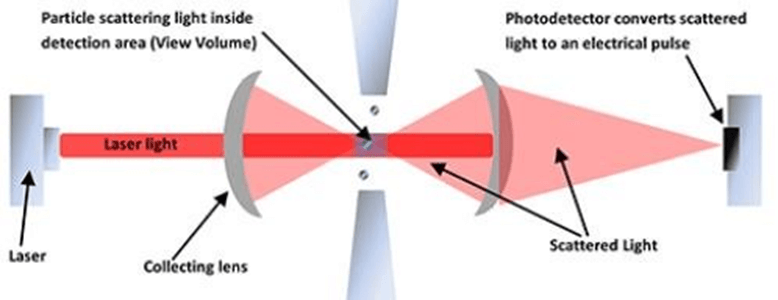
First, a sample is drawn into a sensor using either a needle or sample tube. Then it passes through a laser beam that produces a certain amount of light. The “shadow” cast by the particle allows the light-sensitive detector to determine the size and number of particles in question! For convenience, a liquid particle counter typically converts the output data into a measurable diameter.
To use light obscuration for testing, you need a sample volume of 25ml. For LVP and SVP units, you might have a volume of 25ml or more. In response, the USP <788> requires the use of a “statistically sound sampling plan”. Additionally, “sampling plans should be based on consideration of product volume, numbers of particles historically found to be present in comparison to limits, particle size distribution of particles present, and variability of particle counts between units.”
With proper justification, the USP <788> also allows for the total number of tested units in any given batch to be less than 10 units. The USP <788> dictates a testing range of ≥10 and ≥25 μm. But liquid particle counters have a wider range of sizing, ranging from 2μm to 200μm.
To complete the test, your liquid particle counter will withdraw three samples of at least 5ml and calculate the average cumulative counts, average differential counts, average cumulative counts per ml, and average differential counts per ml. Your liquid particle counter should omit data from the initial run.
What Liquid Particle Counter Is Right For You?
When looking for a liquid particle counter, you want to keep a few things in mind:
- Does the liquid particle counter have the ability to adapt to updated guidelines?
- Will it be able to measure particles in the correct specifications?
- What integrations are available?
- Do you have the manufacturer’s support?
- Does the liquid particle counter make your life easier?
At the end of the day, you want a liquid particle counter that is working for you and improving your cleanroom experience. It is the final line drawn between you and contamination.
That is why we’ve developed the LS-20 Batch Sampler. It is the culmination of over 40 years of working with industry professionals to recognize their needs before even knowing what they are. It’s designed to not only detect the smallest of particles but also make your life easier and solidify your contamination control strategy.
Want a hassle-free, no-obligation demonstration? Let us know – we’ll set it up.
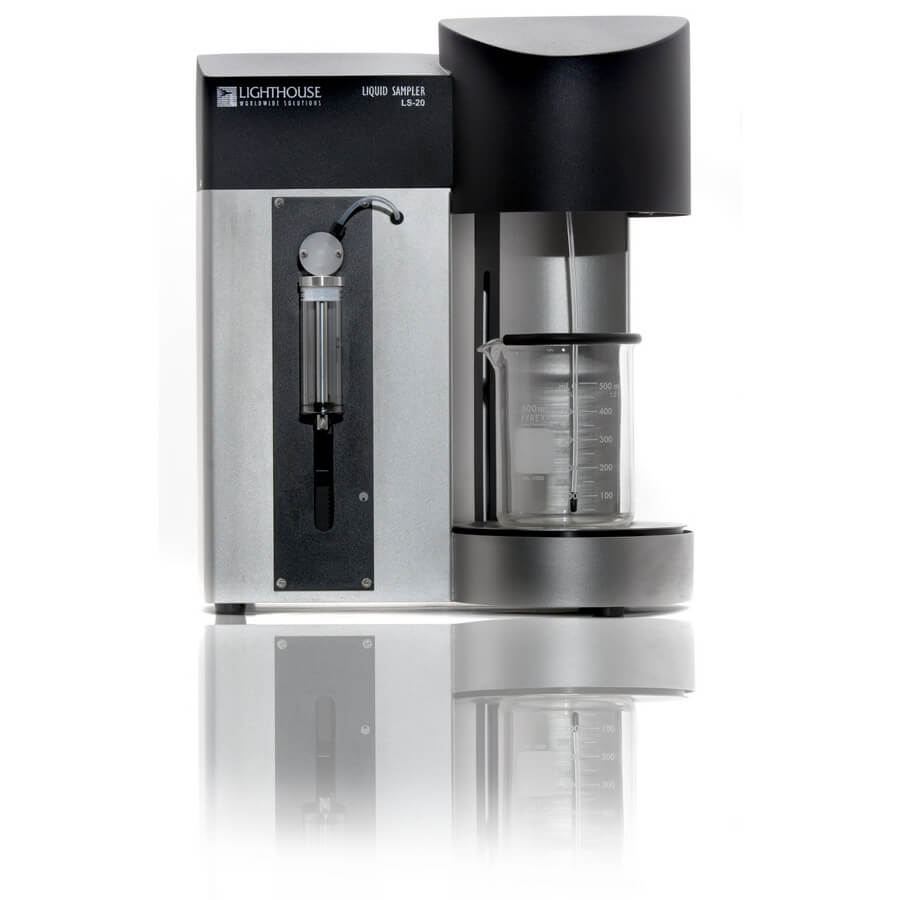